מאת: יפעת זר, מדור ידע וחדשנות המוס"ל
תאריך:13/02/2025
מבוא
מנהלי בטיחות המזהים את שורשי בעיות הבטיחות בארגוני עבודה יכולים לשפר משמעותית את רמת הבטיחות והבריאות בארגון. המאמר מציג תשע שיטות יעילות לניתוח שורשי הגורמים לבעיות הבטיחות (RCA-Root Cause Analysis), השלבים ליישומן ותרחישי דוגמה הממחישים את פעולתן.
מהו "ניתוח שורשי הגורמים "?
"ניתוח שורשי הגורמים" (RCA) הוא תהליך המשמש לאיתור הגורמים הבסיסיים לאירוע, לשגיאה או לבעיה. התהליך מסייע להגיע לליבת הבעיה. במקום להתייחס רק לתסמינים הנראים של הבעיה, ממשיכים לשאול "למה?" כדי לזהות את שורשי הגורמים לבעיה. זה מאפשר ליישם פתרונות המכוונים למקור הבעיה ולא רק אל פני השטח שלה. ביצוע ניתוח גורמי השורש זמן קצר לאחר אירוע, לפני ששוכחים את פרטיו, מספק את המידע המדויק ביותר.
להלן דוגמאות לעיתוי ביצוע "ניתוח שורשי הגורמים":
- לאחר פציעה או מחלה במקום העבודה
- לאחר תקלה בציוד הקשור לבטיחות
- לאחר שפיכה או שחרור של כימיקלים
- לאחר תאונת דרכים
- לאחר תקרית בטיחות או הפרת כללי בטיחות
- לאחר "כמעט ונפגע"
להלן תשע שיטות יעילות לניתוח שורשי הגורמים:
1. חמשת ה"למה"
בשיטה קלה לביצוע זו שואלים שוב ושוב, חמש פעמים, "למה ?" כדי להתעמק בשורש הבעיה, מנסים ל"קלף" את כל שכבות תסמיני הבעיה ולהגיע אל מקורה.
תרחיש לדוגמה:
עובד שעסק בפריקת מלאי ציוד, נפצע כשנפל עליו קופסה כבדה.
שאלה 1 - מדוע העובד נפצע? כי נפלה עליו קופסה כבדה.
שאלה 2 - למה הקופסה נפלה? משום שהקופסה לא הייתה יציבה על המדף.
שאלה 3 - מדוע הקופסה לא הייתה יציבה? כי היא הייתה מונחת ב"מערום" לא תקין.
שאלה 4 - מדוע הקופסה "נערמה" בצורה לא נכונה? מכיוון שהעובד לא פעל לפי הנוהלים.
שאלה 5 - מדוע העובד לא פעל על פי הנוהלים? משום שהעובד לא הוכשר כראוי לשיטות "הערמה" בטיחותיות.
כלומר, הסיבה לפציעת העובד – לא נערכה הדרכת עובד. הפתרון לבעיה - ביצוע הכשרה / הדרכה ל"הערמה" בטיחותית.
2. דיאגרמת "עצם הדג" (תרשים אישיקאווה)
ישנו "עמוד שדרה" אופקי המוביל ל"עצמות" אלכסוניות, המתפצלות ממנו ומייצגות סוגים שונים של סיבות.
השלבים לשרטוט דיאגרמת "עצם הדג":
- רשום את הכשל בצד ימין כ"אפקט".
- צייר חץ אופקי ימינה אל ה"אפקט" .
- קבץ סיבות עיקריות לקטגוריות, כמו, כוח אדם, טכנולוגיה, תהליכים וכדומה.
- רשום גורמים עבור כל קטגוריה באמצעות "למה זה קורה" כדי לחקור את הסיבות השורשיות.
- חזור על השאלה "מדוע" עבור כל סיבה כדי לחשוף גורמים עמוקים יותר.
- נתח את הדיאגרמה עבור דפוסים ואזורים טעוני שיפור.
- לאחר השלמת התרשים, זהה דפוסים במידע וקבע אילו חלקים טעונים שיפור.
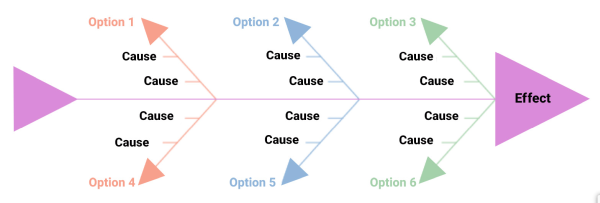
3. ניתוח מצבי כשל ואפקטים (FMEA- Failure Mode and Effects Analysis)
ניתוח מצבי כשל ואפקטים (FMEA) היא טכניקה שיטתית לזיהוי כשלים פוטנציאליים בתכנונים, בתהליכים ובשירותים לפני שהם מתרחשים בפועל. מטרתו היא למנוע כשלים על ידי בחינת האופן שבו כשלים עלולים להתרחש וההשפעות שיכולות להיות להם.
השלבים ליישום FMEA:
- הרכב צוות רב תחומי המכיר את התהליך.
- צור מפת תהליכים המציגה את כל השלבים בפירוט.
- עבור כל שלב, ערוך סיעור מוחות על מצבי כשל פוטנציאליים והשפעותיהם, בו יש לשקול:
כיצד יכול השלב בתהליך להיכשל? מה תהיינה ההשפעות אם אכן ייכשל?
- דרג את חומרת ההשפעות של כל מצב כשל (למשל 1-10).
- קבע את הסיבות ואת תדירות ההתרחשות עבור כל מצב כשל.
- חשב את רמת הסיכון (RPN - risk priority number) על ידי הכפלת רמות החומרה, ההיארעות והזיהוי.
- תעדף מצבי כשל RPN גבוהים לפעולה מתקנת.
- יישם ואמת פעולות מתקנות.
- המשך לעקוב אחר RPNs ומצבי כשל חדשים ב-FMEAs עתידיים.
דוגמה ליישום FMEA:
הנושא |
איסוף מידע |
כשל פוטנציאלי |
לא התקבל מידע 3 שבועות לפני תאריך ה"דד-ליין" |
השפעות פוטנציאליות של הכשל |
שיבוש המשך תהליך העבודה |
חומרה (1-5) |
2 |
גורמים אפשריים |
PI לא ענה על השאלות במדויק ובזמן |
שיעור האירעות |
5 |
אמצעי שליטה ובקרה |
כלים מקוונים לקביעת ה"דד ליין" |
זיהוי |
1 |
RPN |
10 |
פעולות מומלצות |
הודעת אימייל על איחור |
פעולה שננקטה |
|
4. ניתוח "עץ תקלות / שגיאות " (Fault Tree Analysis)
ניתוח עץ שגיאות (FTA) הוא סוג של ניתוח כשל לוגי שמנסה להתחקות אחר הסיבות להתרחשות אירוע בעייתי, שנקרא "האירוע העליון". בשיטה זו ישנה הצגה וויזואלית של כל הדרכים היכולות להוביל לאירוע, באופן המאפשר לצוות הבטיחות להבין היכן ייתכן שיהיה צורך במחסומים חזקים יותר או באמצעי בקרה למניעה.
השלבים בניתוח "עץ תקלות"
- הגדר את ה"אירוע העליון" והבלתי רצוי הספציפי לניתוח.
- זהה סיבות מידיות כצמתים ראשיים בתרשים עץ התקלה.
- קבע סיבות משניות לכל סיבה ראשונית.
- הוסף שכבות של סיבות וחבר אותן עם שערים לוגיים (AND, OR וכו').
- נתח את עץ התקלה עבור סיבות נפוצות ואזורים לשיפור.
אפשר לכמת את עץ התקלה על ידי חישוב ההסתברות ל"אירוע העליון" בהתבסס על שיעורי הכשל ברכיבים שלו.
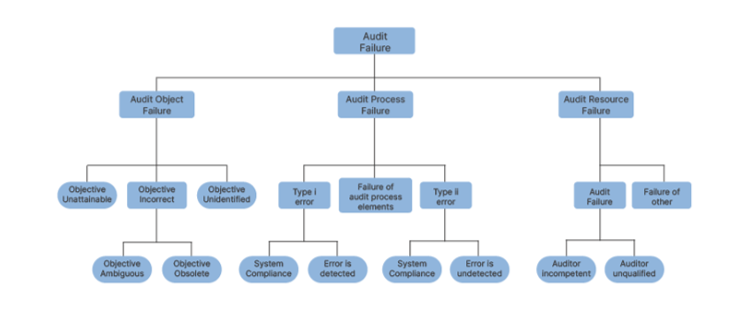
תרחיש לדוגמה
בחינת "אירוע עליון": פציעת עובד מזרוע רובוטית על פס הייצור. הסיבות העיקריות האפשריות הן "זרוע רובוטית פוגעת בעובד" ו"עובד בטווח הזרוע". סיבה משנית ל"עובד בטווח הזרוע" יכולה להיות "העובד נכנס לאזור ללא אישור". ככל שעץ התקלות ממשיך לסיבות המשניות, הוא מאפשר למפות את כל הסיבות האפשריות שעלולות לגרום לעובד להיפצע מהזרוע הרובוטית ולזהות חולשות במחסומי בטיחות, הדרכה, תחזוקת ציוד, אזעקות ונושאי מפתח אחרים. הרעיון הוא להפחית את ההסתברות שהאירוע העליון הבלתי רצוי יתרחש על ידי הפחתת ההסתברות לאותן תקלות המופיעות ב"מורד" העץ.
5. ניתוח "פארטו" (Pareto Analysis)
עקרון ה"פארטו", הידוע גם בתור כלל 80/20, מבוסס על כך ש-80% מהתוצאות נובעות מ - 20% מהסיבות. ניתוח Pareto כולל סיווג הסיבות השונות לאירועי הבטיחות וקביעת תדירות התרחשותן ועוזר לזהות את הגורמים התורמים באופן המשמעותי ביותר לאירועי בטיחות.
השלבים ליישום ניתוח "פארטו"
- אסוף נתונים על אירועי בטיחות, כולל סיבות ותדירות.
- דרג את האירועים לפי תדירותם.
- חשב תדירות מצטברת ושיעורי היארעות עבור כל סיבה.
- צור תרשים "פארטו" בו הסיבות בציר ה-x והתדירות בציר ה-y.
- זהה את הגורמים המרכזיים - העיקריים (Vital Few) לפי התרשים.
- התמקד בטיפול בגורמים מרכזיים אלה כדי לצמצם את אירועי הבטיחות.
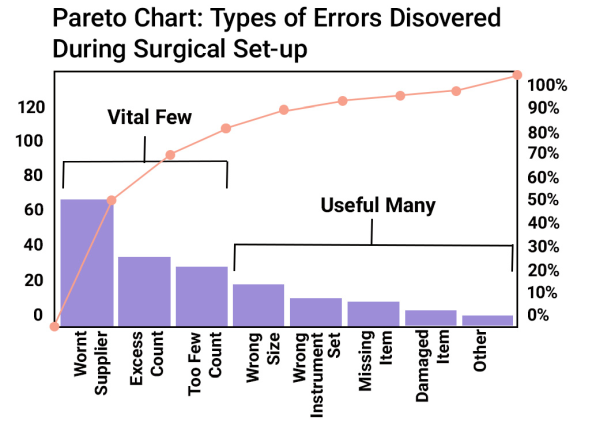
תרחיש לדוגמה
אתר בנייה סקר את נתוני אירועי הבטיחות שאירעו בו ויצר תרשים "פארטו". התגלה שהחלקות, מעידות ונפילות היוו 70% מכלל התקריות. מפגעי חשמל ואירועי struck-by היוו 20% מהתקריות ו - 10% הנותרים היו אירועים קלים אחרים. מיקוד משאבי הבטיחות של מנהלי אתר הבניה בהפחתת החלקות, מעידות ונפילות הוביל לשיפור הבטיחות באתר. מפגעי חשמל ומפגעי struck-by טופלו גם הם, אך במידה פחותה יותר.
6. ניתוח "עניבת פרפר" (Bowtie)
"ניתוח עניבת פרפר" היא שיטת ניהול סיכונים הממפה ויזואלית את התהליכים המובילים להתרחשות סיכון ("קשר הפרפר") ואת ההשלכות שלו. כאשר הסיבות והתוצאות לאירוע הסיכון המרכזי ממוקמות משני הצדדים שלו בתרשים, נוצרת "עניבת פרפר". ניתוח Bowtie מראה את כל משתני הסיכון, מאפשר ליצור תרחישים של "המקרה הגרוע ביותר" (Worst Case Scenario) במקום העבודה ויכול לסייע לצוותי הבטיחות לזהות את הסיבות לאירועי בטיחות ואמצעי בקרה חיוניים כדי להפחית את שיעור אירועי הבטיחות.
השלבים ליצירת ניתוח "עניבת פרפר"
- זהה את אירוע הסיכון הקריטי (המרכזי) או המפגע ("קשר הפרפר").
- מפה איומים פוטנציאליים וגורמים המובילים לאירוע הסיכון (צד שמאל).
- זהה השלכות ותוצאות פוטנציאליות של אירוע הסיכון (צד ימין).
- הוסף, מצבי כשל ספציפיים, למטה בשני הצדדים.
- הוסף אמצעי בקרה ושליטה קיימים ומוצעים.
תרחיש לדוגמה
מתקן ייצור תעשייתי מעוניין לנתח את אירוע הסיכון הפוטנציאלי של דליפת כימיקלים מסוכנים. מנהלי המתקן יוצרים תרשים "עניבת פרפר" עם "שפך כימיקלים" בתור "קשר הפרפר". בצד שמאל, נרשמים גורמים כמו, קורוזיה של מכלי אחסון הכימיקלים, שגיאות של עובדים בטיפול ותקלות של ציוד. בצד ימין, נרשמים השלכות האירוע, כמו, אדים רעילים, זיהום של האזורים בסביבה, פציעות עובדים ונזקים סביבתיים. מוסיפים רישום בקרות קיימות, כמו ציוד מגן ופרוטוקולי תגובה לדליפת הכימיקלים.
הניתוח מספק תוכנית מפורטת לניהול סיכונים ומדגיש את הצורך בבדיקה ובניטור נוספים של מכלי הכימיקלים כנקודת בקרה קריטית.
7. פתרון בעיות D8
שיטת פתרון בעיות D8 היא גישה מובנית מבוססת צוות לזיהוי שורשי בעיות ונקיטת אמצעי תיקון למניעת הישנותן. ה-"D8" מתייחס לשמונה התחומים או השלבים המתודיים הנדרשים כדי לטפל בבעיות בצורה שיטתית. בשיטה זו נפגשים חברי צוות ממחלקות ומתפקידים שונים ומעלים מגוון תובנות ואפשרויות למציאת שורשי הבעיות.
דוגמה לתרחיש ויישום של פתרון בעיות D8
עובד נפצע כאשר נפל עליו מטען כבד שהיה מאוחסן באופן לא בטיחותי על מדף גבוה. ניתן להקים צוות D8 שינתח את האירוע הזה.
D1: הרכבת צוות - מנהל בטיחות, מנהל מחסן, איש תחזוקה והעובד שנפצע.
D2: הצוות מפתח הצהרה מפורטת של הבעיה, המתעדת את האירוע.
D3: בינתיים, מפרסמים איסור לאחסן מטענים כבדים על מדפים גבוהים.
D4: על ידי ראיון צוות העבודה ובדיקת אזור האחסון, מזוהה גורם השורש של הבעיה - עומס כבד של מטען המונח באופן לא בטיחותי על המדף.
D5: פיתוח נוהל עבודה חדש לאחסון בטיחותי של מטענים כבדים.
D6: כל הצוות עובר הכשרה לנוהל החדש.
D7: המדפים עוצבו מחדש כדי למנוע עומס יתר.
D8: הצוות מקבל אישור על עבודתו לשיפור בטיחות האחסון.
8. מפת שורש
מיפוי שורש הוא דיאגרמה ויזואלית המתארת את הקשר בין בעיה או פגם לבין הגורמים הסיבתיים הבסיסיים שלה. הוא מספק תמונה ברורה של האופן שבו אלמנטים שונים מתחברים יחד, חיבור המוביל להשפעה לא רצויה.
השלבים ליצירת מפת שורש:
- ציין בבירור את הבעיה בחלק העליון או השמאלי של המפה.
- רשום את כל הגורמים התורמים הפוטנציאליים כענפים היוצאים מהבעיה.
- עבור כל ענף, שאל "למה זה קורה?" כדי לזהות גורמי משנה.
- השתמש בקווים ובחצים כדי להראות מערכות יחסים וכיוון השפעה.
- חפש דפוסים חוזרים. גורמי השורש ימצאו לרוב בתחתית המפה.
- הצע פתרונות לטיפול בגורמי השורש שנמצאו.
תרחיש לדוגמה
פועל מחליק ונופל על רצפה רטובה בסמוך לכניסה לבניין. כדי לנתח את האירוע, מייצרים מפת שורש. אירוע הנפילה נרשם כבעיה. גורמים תורמים, כגון, מזג האוויר, מצב הרצפה, נעלי העובד, הסחת דעת ותאורה, נחקרים באמצעות ענפי משנה. המיפוי חושף גורמי שורש, כמו משטחי עבודה לא בטיחותיים, ניקוז לקוי, היעדר כללי בטיחות וכו'. אפשר להתמקד בגורמים אלו במציאת פתרונות לבעיה.
9. ניתוח שינויים
ניתוח שינויים הוא טכניקת ניתוח שורש הכוללת השוואת מצב - לפני ואחרי התרחשות השינוי. המטרה היא לזהות את הסיבות השורשיות לשינוי בתוצאות.
השלבים לביצוע ניתוח שינויים:
- זהה את השינוי המוביל לתוצאה הבלתי רצויה (תהליך, ציוד, כוח אדם וכו').
- אסוף נתונים לפני ואחרי השינוי, בהתחשב בכל המדדים הזמינים.
- השווה נתוני לפני ואחרי כדי לזהות הבדלים.
- נתח הבדלים כדי לאתר גורמי שורש פוטנציאליים.
- ערוך סיעור מוחות על ידי העלאת השאלה - מה השתנה.
- קבע גורמי שורש סבירים בהתבסס על ראיות ונתונים.
תרחיש לדוגמה
לאחרונה, בוצע שדרוג של מתקן ייצור תעשייתי. ציוד ידני הוחלף בציוד אוטומטי. מאז השינוי חלה עלייה בשיעור הפגמים במוצר. כדי למצוא את גורמי השורש, נעשה שימוש בניתוח שינויים כדי להשוות מדדים של לפני ואחרי שדרוג הציוד:
- שעות ההפעלה: ירידה מ-60 שעות בשבוע ל-40 שעות בשבוע
- נפח הייצור: גדל מ-1,000 יחידות ליום ל-1,500 יחידות ליום
- שיעור הפגמים: עלה מ-2% ל-5%
על ידי ניתוח השינויים בנתונים, מזוהים שני גורמי שורש פוטנציאליים:
- מפעילי הציוד האוטומטי החדש לא קיבלו הכשרה להפעלתו.
- הגברת מהירות הייצור הובילה לפגמים בייצור.
חקירה נוספת תקבע מהו הגורם העיקרי בו יש להתמקד.
מקור: